In October, a new lining milestone was established by our US-based crew with the installation of a 12‑inch x 213 m (700 ft) ALTRA10, Class IV, fully structural cured-in-place pipe (CIPP) under Interstate 89 in South Burlington, Vermont. The previous installation milestone was in Foxborough, Massachusetts in 2018, with a 12‑inch x 185 m (607 ft) installed liner.
The water main needing to be renewed was an aging 12 inch asbestos cement (AC) and cast‑iron (CI) pipe, which was set in, and somewhat supported by, a 36-inch concrete carrier pipe.
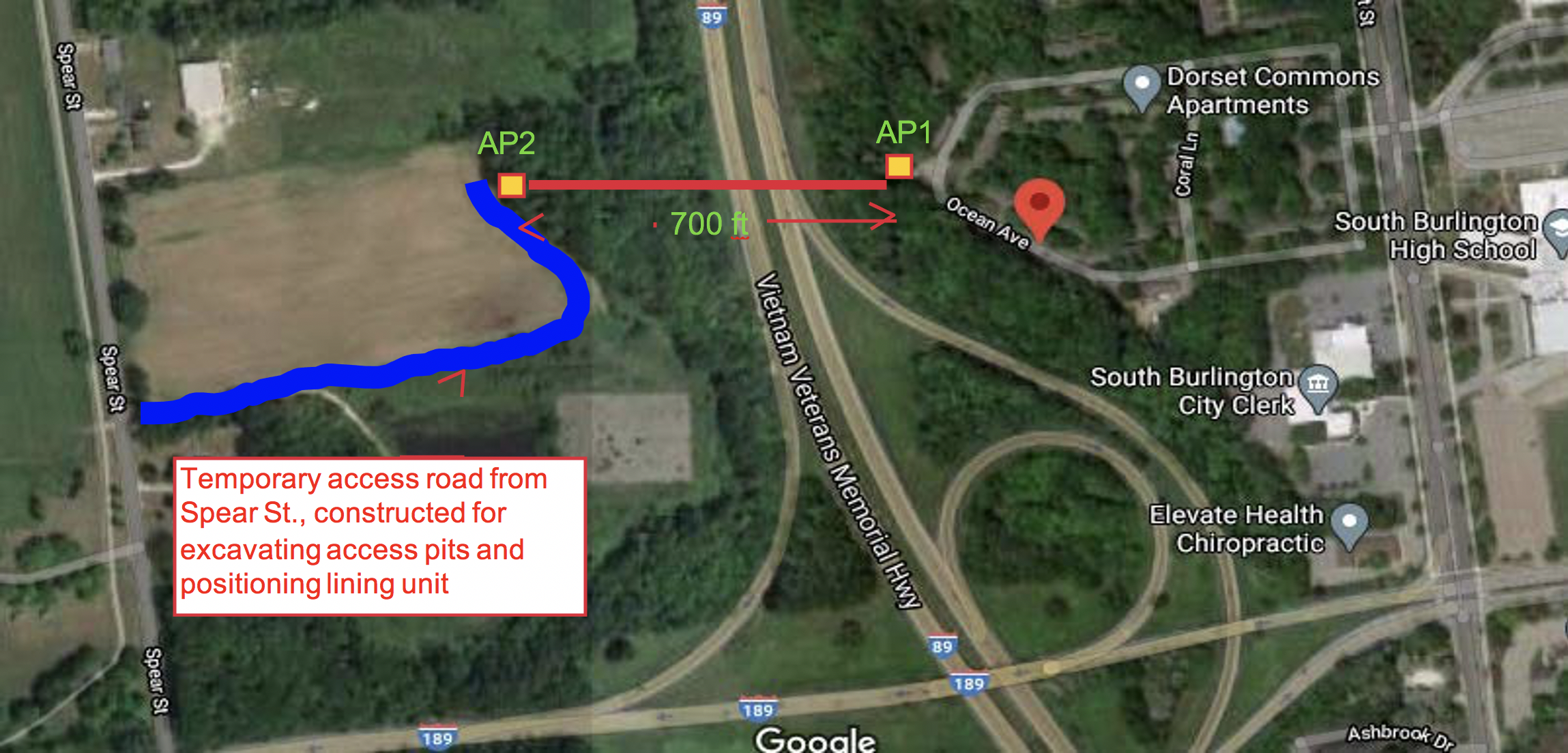
Aerial view of project location in South Burlington, VT
Many of the standard challenges were exercised and coordinated with the City of South Burlington’s Public Works Department and the engineering firm overseeing the project (Aldrich + Elliott, PC) to prepare and implement site-specific requirements for the mobilization and staging of LOGISTEC Environment’s mobile lining units, such as creating a temporary access road off Spear Street and adjacent to a landowner’s field, making it possible for the crew to drive the lining unit to the second access pit, located on the opposite side of I-89. Since the project was also set in a sensitive migratory bird conservation area, it was necessary to adhere to guidelines minimizing environmental disruption and impacts to the area.
For these same concerns, many cities like South Burlington are now seeking alternatives that eliminate the need for the traditional dig and replace method, which is more disruptive than installing structural liners, as well as the associated costs and concerns raised with site remediation and the disposal of AC water mains.
The main issues with these site-specific special projects under highways/railroads and rivers are associated with special permitting and easement concerns, as well as the disposal of the water used in our cleaning and curing process, which is generally directed to a storm drain or manhole. With this specific installation under I‑89, it was also impossible to create a loop to recirculate the hot water to the boiler unit. As such, additional water capacity was required in the form of a tanker truck to supplement our heated water storage tanks located inside the boiler unit. This calculated water volume must be doubled, and sometimes tripled, in order to fully cure the liner in a closed‑loop set‑up, where the outlet valve is slightly open, while maintaining standard operating pressures, and mitigate water leakage throughout the complete curing process.
The end result was deemed a success, with a fully‑cured and pressure‑tested/inspected 12-inch x 700 foot structural liner installed within 5 days.